LX Group discusses the 4-20mA Current Loop
There are many methods of sending data between sensors and devices that require the data, and many newcomers to the industry may be aware of the usual digital data buses such as Serial Peripheral Interconnect (SPI for short) or the Inter-Integrated Circuit bus (known as the IIC or I2C bus). Although they are popular and many devices are available that communicate using these methods, they have several downfalls which can preclude them from some applications. These can include distance – the I2C bus requires repeater ICs fitted along the run after around 20 metres, and care must be taken to ensure the bus capacitance level stays below a certain amount; and interference – any digital signal is susceptible to interference from a variety of sources.However there is a method of transferring signals and data that is both much simpler to understand and also reliable over long distances – the “4-20mA Current Loop”. This has been used successfully over many years to report analogue values back to a host system from a sensor and also transmit digital data (however not at any great speed).How the “loop” (as we will now call it for brevity) works is very simple to understand – a DC current loop is formed with a power supply of between 12 to 40 VDC, with the sensor or device in series with system analysing the loop then back to the power supply, for example:
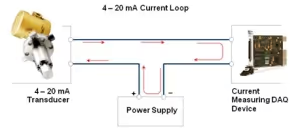
(Image courtesy National Instruments)
The device or sensor (such as the transducer in the image above) is powered by the current in the loop, which is convenient as seperate power runs are not required – saving installation cost and maintenance time.The data gathered by the sensor is translated to a level of current flow, thus controlling the current flowing through the loop – which will fall between a range of four and twenty milliamps. Finally, the device at the end of the loop can simply measure the current using a simple analogue-to-digital converted and process as normal. This is therefore a method of transmitting either analogue or digital data.Some systems can also transmit digital data at a slower speed, by simply turning the current on and off in a similar manner as basic logic systems – and although generally used by telegraph and telex systems in the previous century, there may still be applications for this in the future when no other wired alternative is possible. An example of this may be adding new sensors to an existing building with existing wiring that cannot be accessed completely for replacement or heritage reasons.Almost any type of device that uses a current signal to transmit data can be used on the “loop”, such as position or rotation sensors – ideal for remotely monitoring a machine’s RPM or physical position; environmental sensors such as vibration, humidity and temperature; tank liquid level sensors – and many more. And the system makes troubleshooting quite simple – if current isn’t flowing in the loop, your system can alert to a faulty sensor or line immediately.It is also possible to run more than one loop from a power supply, as long as each loop is in parallel and the power supply can source the total amount of current required by the individual loops, and that the systems measuring the current are in series with the device in its’ unique part of the loop. Furthermore some engineers have also been able to power other mutually-exclusive devices from the loop – such as ultra-low power TI MSP430 microcontrollers, as long as the current drawn by the new device falls within the tolerance of measurement by the end system. This method has also proved popular by those wishing to upgrade sensor networks without adding or replacing any existing wiring runs.Thus it can be said that the 4~20 mA current loop system may not be the “latest technology”, but it can effectively solve problems in the right circumstances. However there are many options, and choosing the right one is a fundamental step for the success of your project. So if your design team is set in their ways, or you’re not sure which data communication method is best for your application – it’s time to discuss this with independent, experienced engineers.At the LX Group we have experience designing a wide range of data gathering and control systems over short and long distances – and using this experience we can determine the most effective method of returning data and control signals no matter the application or geography. Our engineering team have developed a number of systems in this area and have extensive experience with the core technology requirements of such systems.We understand the importance of high availability, accuracy and integrity of the systems, combined with the need for future proofing infrastructure rollouts. For more information or a confidential discussion about your ideas and how we can help bring them to life – click here to contact us, or telephone 1800 810 124.LX is an award-winning electronics design company based in Sydney, Australia. LX services include full turnkey design, electronics, hardware, software and firmware design. LX specialises in embedded systems and wireless technologies design. www.lx-group.com.auPublished by LX Pty Ltd for itself and the LX Group of companies, including LX Design House, LX Solutions and LX Consulting, LX Innovations.